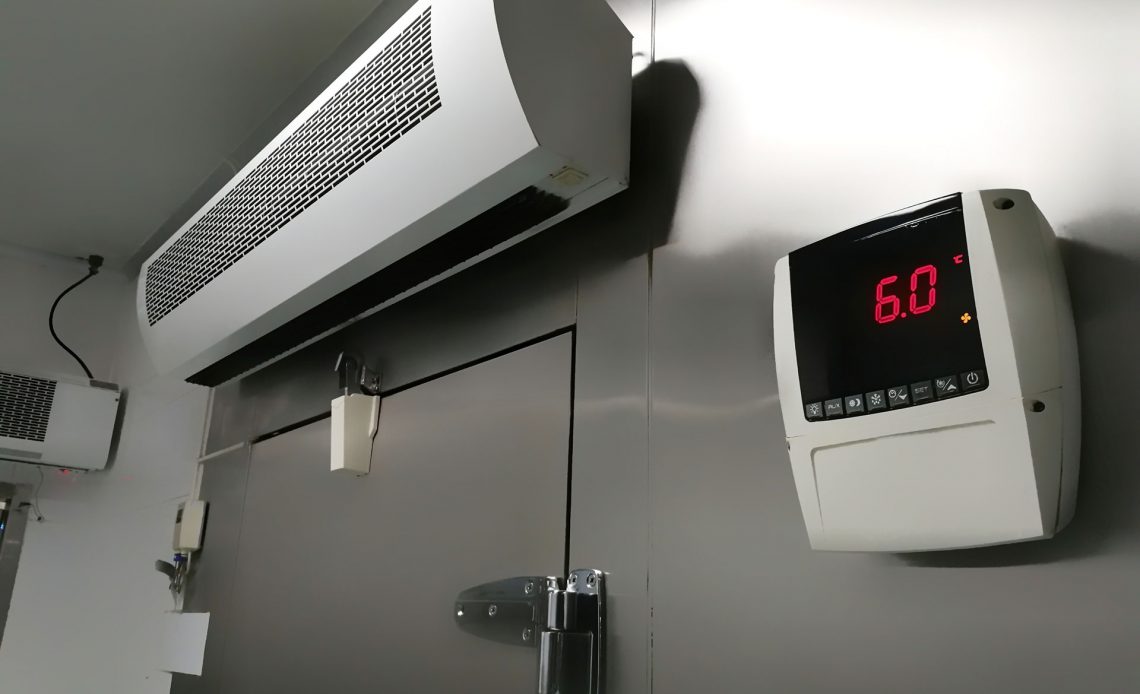
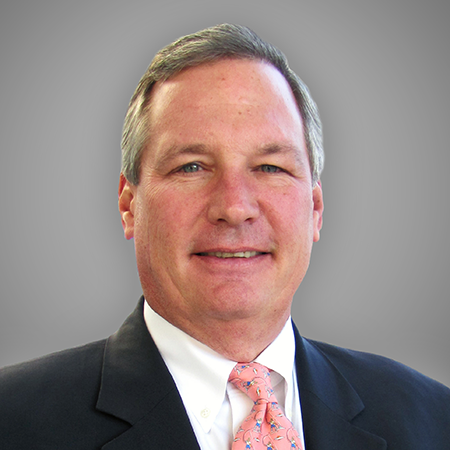
Steve Kozarits
Senior Vice President
Chicago
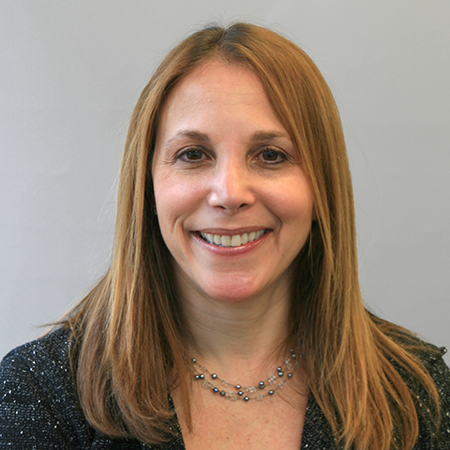
Lori Zuck
Managing Director
Florham Park
Our attitudes about food and beverage influence the brands we purchase, how we socialize, where we shop – and sometimes even where we live. Our expectations are high when it comes to product mix and availability. When our wants and needs are not met quickly, as was the case at the start of the pandemic, we are highly dissatisfied. While food transport has been occurring for centuries, modes of delivery, advances in food safety and time-sensitive supply chains have evolved to meet the changing desires of consumers across increasingly broad geographies. Often, new trends become ingrained habits that can alter consumer behavior and ultimately drive monumental business decisions.
And that is how cold storage became one of the hottest topics in the commercial real estate industry.
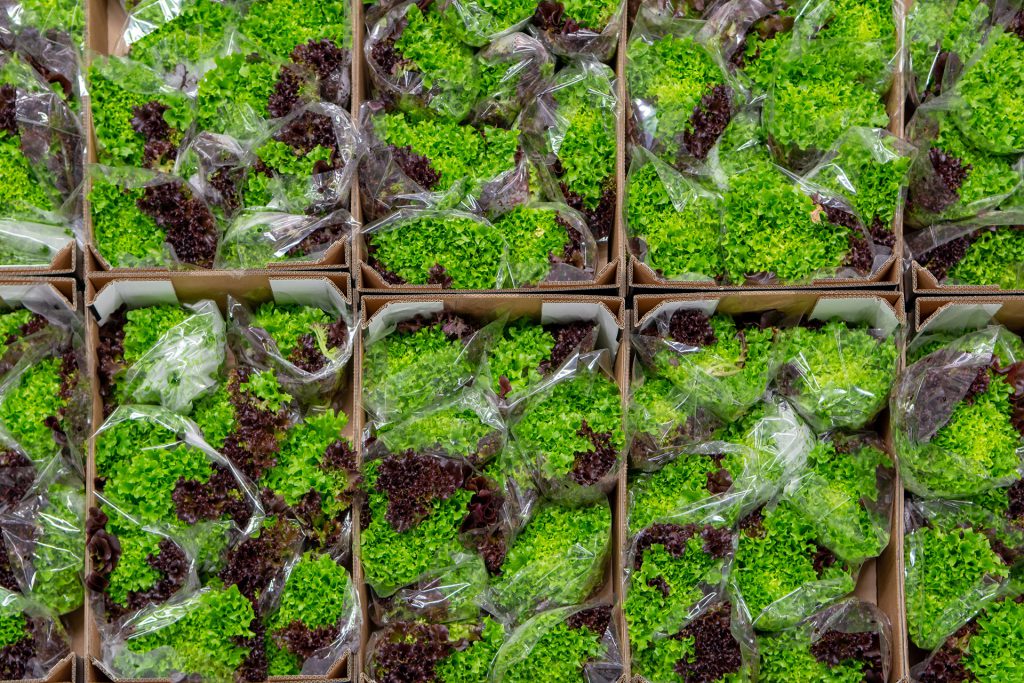
Defining the sector
The global cold chain consists of two primary subsectors: refrigerated storage and refrigerated transportation, with the former making up a larger share of the market. Overall, the value of the sector is estimated at $218 billion for 2020 and is expected to reach $320.2 billion by 2025, according to a June report from VynZ Research. North America is the second-largest cold chain market, as the U.S. is home to the most major players worldwide.
More institutional investors feel that cold storage is a safe bet for their capital, and occupiers are clamoring for modern space in key geographies.
This industrial niche is exploding due to a confluence of factors. First, growing demand for food and beverage through e-commerce channels – which was greatly intensified during COVID-19 – shows no sign of abating. With many having more time to browse online at home, shopping habits ingrained over the past six months will likely stick for a good portion of the population, and this requires strict preservation safeguards to avoid health hazards. At the same time, consumers’ preference for more natural foods with fewer chemical preservatives requires increased dependence on refrigeration for product transportation and storage.
Not content with the status quo
Even with the many advances cold storage has enjoyed, there remains intense focus on increasing efficiencies, lowering costs and building flexibility into the distribution centers equipped to store food and beverage. This is true especially today, when e-commerce is not only powered by convenience but also by a heightened sense of health amid a pandemic.
The challenge is twofold: Like all e-commerce, getting product to consumers quickly is vital in meeting expectations for instant gratification, but even more important is ensuring the quality and safety of what is delivered. At present, occupiers are clamoring for modern cold storage space in key geographies to meet skyrocketing demand – especially related to grocery delivery – while more institutional investors feel comfortable that cold storage is a safe bet for their capital investment. In fact, as the majority of new product is either build-to-suits with long-term leases or owner occupied, this sector has begun to attract a new group of investors focused on credit and term in addition to location.
Adoption of this highly specialized product type was not unanimously embraced at the onset. Like every real estate sector, cold storage presented pros and cons. On one hand, grocery stores generate low profit margins and must rely on volume. Overhead costs – especially labor – are high, so pushing an e-commerce solution made sense. On the other hand, refrigerated storage facilities are expensive to build, costing at least twice as much per square foot as traditional warehouses. Once complete, they are expensive to operate because facilities are energy hogs and experience no downtime. And once these facilities are built, their unique characteristics may not be suitable for subsequent users.
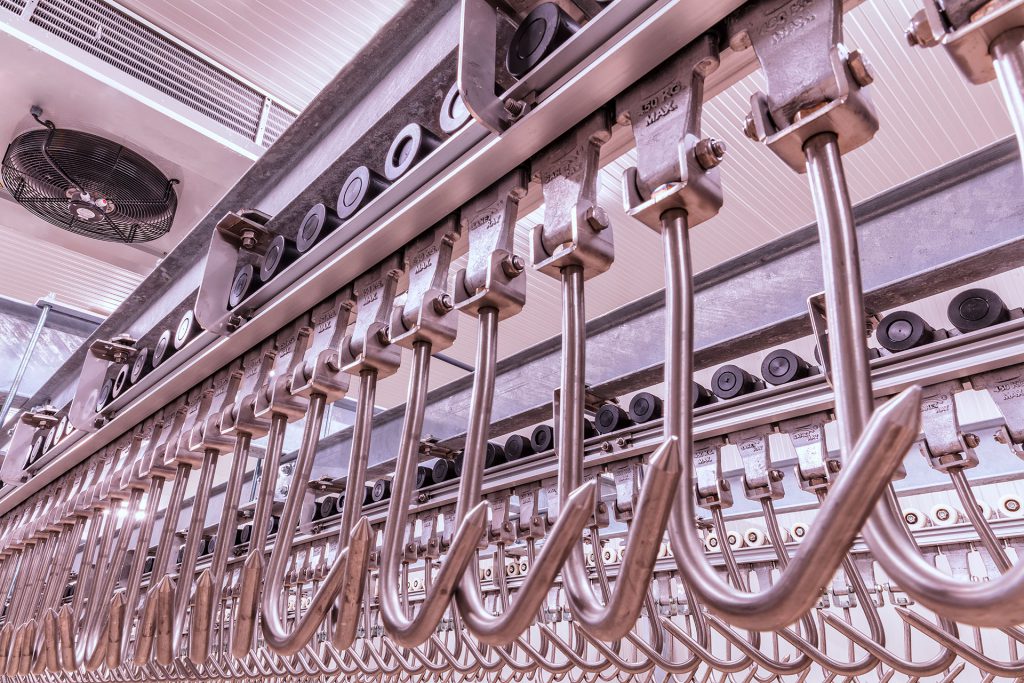
Challenges met with innovation
Creative solutions have been rapidly incorporating efficiencies and cost controls to make cold storage a true gamechanger for owners and occupiers.
Investors want to build new cold storage facilities, but where?
Last-mile delivery sites are already in high demand and land is scarce. But ground-up construction is not always necessary. As grocery stores continue to experience weaker-than-historical walk-in traffic, expect to see a shift as some existing stores transition into cold storage distribution centers. This makes sense: Most assets are in high-density population centers and are prime candidates for “box in a box” redevelopment. However, the economic benefits of a conversion do not always materialize, so careful cost/benefits analysis is important.
Similarly, older malls in areas with strong demographics can be repurposed to support the needs of cold storage, creating value that may far exceed an asset’s use as conventional retail space. Millennials are not attracted to malls the same way their parents and grandparents were in their prime shopping years, but location can influence the ongoing success of physical space that offers good transportation options and easy access to consumers.
Users want higher ceiling heights, but how?
A relatively new fire suppression solution called an Oxygen Reduction System (ORS) has the potential to significantly reduce costs in cold storage and other warehouse facilities that exceed certain clear heights. ORS technology eliminates the need for traditional sprinkler pipes, which restrict ceiling heights to 50 feet or less, and creates a low-oxygen environment for buildings of any ceiling height. Hence, an asset can offer 120-foot clearance without affecting the cost-per-pallet position.
Future implementation of ORS will depend on whether fire marshals in local municipalities trust and approve use of this budding technology, but it shows promise. Another challenge is that this environment is unsuitable for humans, and workers must carry oxygen with them when entering the facility to perform maintenance or inspections. Fortunately, other advances – most notably automated storage and retrieval systems (ASRS) – are helping to address the issue of worker safety.
Facilities must keep labor costs in check, but by what means?
Some degree of automation is common in all industrial facilities, and cold storage is no exception. If humans can’t function in a low-oxygen environment, or employee density must be reduced for health and safety reasons, bring in “cobots,” or collaborative robots. A study by Interact Analysis predicts that cobots will account for 30{ff66251fa959225ec0415bec498104472c710c05756e34120ff9c6ac4cef9161} of the total robot market by 2027, and the three biggest applications will be material handling, assembly and pick-and-place.
Owners and users of cold storage space are investing capital to lower energy costs.
For example, Apex Motion Control, a specialist in automation for the baking and food industry, recently announced a new function for its Baker-Bot. In addition to decorating cakes, pick-and-place, and loading/unloading trays and pans, the company’s cobot can now handle palletizing tasks and be integrated into most production lines without the need for safety guarding. And because cobots are flexible and easy to set up, they are attractive to smaller companies which may not have previously considered automation in a warehouse setting.
Sustainability efforts can save money, but will they pay off?
Cold storage facilities must run continuously, making them one of the most energy-intensive property types. As in all sectors of commercial real estate, owners and users of cold storage space are investing capital to lower energy costs and reduce greenhouse gas emissions. This includes incorporation of alternative energy solutions like solar panels, reduction in water usage, and deployment of highly efficient refrigeration systems. United States Cold Storage, one of the four companies dominating this space, harvests rainwater and has reduced GHG emissions by 12{ff66251fa959225ec0415bec498104472c710c05756e34120ff9c6ac4cef9161} while increasing its cubic capacity by 31{ff66251fa959225ec0415bec498104472c710c05756e34120ff9c6ac4cef9161} over the past five years, proving that focused efforts pay off. In the facility itself, automated high-speed doors and advanced sealing materials can further reduce energy loss.
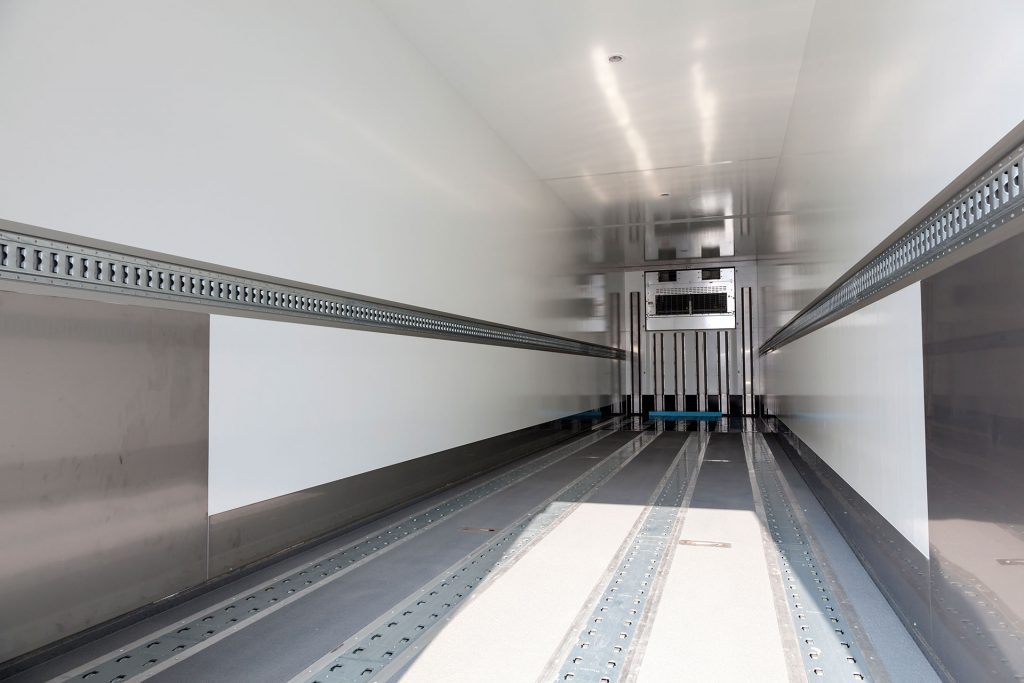
Location decisions also play an important role here. In the Midwest, underground storage is an alternative to above-ground warehouses, though ceiling heights present a limitation. Cave-type facilities, common throughout Kansas, Arkansas and other states, offer low humidity and refrigerator temperatures. Coincidentally, these same conditions also are ideal for the computer power supporting warehouse automation. Across the U.S., there are major differences in utility pricing and economic incentives for sustainability initiatives, so matching facility needs to regions or metros that offer the best economics is key.
Favorable outlook
These innovative solutions bode well for this sector. As recent property sales have underscored, cold storage is not being affected by the general economic slowdown, though the number of operators may shrink as the leaders benefit from economies of scale and compress cold chain costs. It’s also good news for consumers, who have gotten very comfortable choosing their favorite food and beverage items from home. Every problem has a solution, and when the solution supports the goals of all constituents, even better. COVID-19 illuminated challenges and opportunities that will ultimately strengthen cold storage’s performance as an asset class – and industrial infrastructure across the board.